
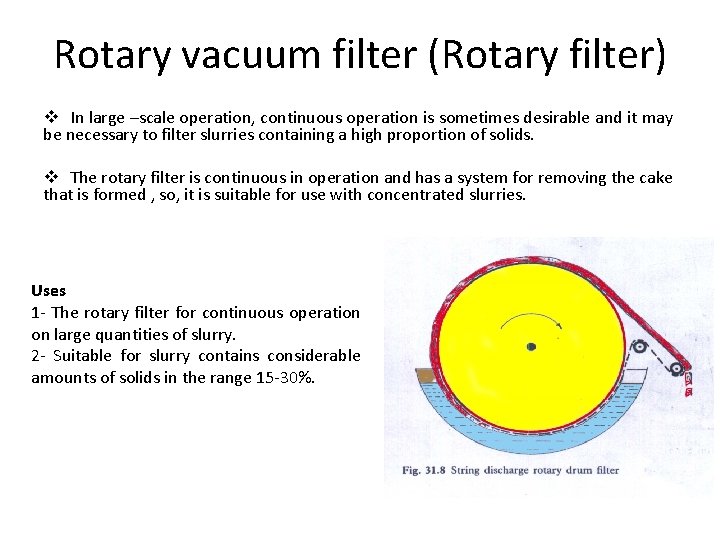
It is optimally suited for all applications where water vapor is expected, such as low temperature sterilization and drying. With the new Pascal 2021 HW, Pfeiffer Vacuum presents the two-stage rotary vane pump with the highest vapor capacity in its class. Ideal for working with aggressive gases.The exchangeable sealing plates are fastened to inherently stable support beams. High-end, chemically resistant plastics, such as, for instance, PE or PEEK, reliably implement the sealing effect. Separation elements pneumatically pressed against the drum reliably separate the individual segment zones from one another in a pressure-tight manner. Depending on the application, the filter cloth is a plastic or metal mesh. The inlays comprise the filtrate discharge mechanism, support tissue and filter cloth. They are connected to the drum via screws on the filter elements. The cell inlays separate solid matter from the suspension. The filter cell contains the cell inlays, which constitute the actual filter element. After cake discharge, a cleaning mechanism takes care of continuous or on-demand filter cloth cleaning. If required, this zone can also be equipped with a gas-tight sealing hood. An autonomously operating scratcher supports cake discharge where necessary. The cake is discharged in a non-pressurized filter zone via air, steam or nitrogen blowback. This allows the collected filtrates and treatment media to be drained independently of each other. A ring space is located between the rotating core and the rigid control head housing isolating plugs subdivide this space into segment zones that correspond to the process zones at the filter. The control head consists of a core that is permanently fastened to the drum. The head also controls blowback for cake discharge and cloth cleaning. The control head is where the respective filtrates are separately drained. Operators can configure the cake thickness to optimize the process. The cells contain the cell inlays, which are covered with the filter medium and screwed to the drum. Separator bars and drum rings subdivide the drum surface into box-shaped cells, which serve to hold the filter cake. The standard operating pressure is 3 bar (g) and up to 7 bar (g) for high-performance filters. The suspension, or the media to be treated, is fed from the outside to the corresponding segment zones under pressure. The separation elements divide the housing into segment zones. We produce special-purpose filters for applications in the pharmaceutical, food and bioprocess industries. We employ high-quality sealing materials and advanced plastics suitable for each application. We utilize different stainless steel grades as required by the specific application scenario. The cake can be discharged to the surrounding area at atmospheric pressure. Cake discharge at atmospheric pressureĮach process step is sealed off into a segment zone by means of pressure-tight separation elements inside of the rotary pressure filter. This enables the procedural optimization of each individual process step.
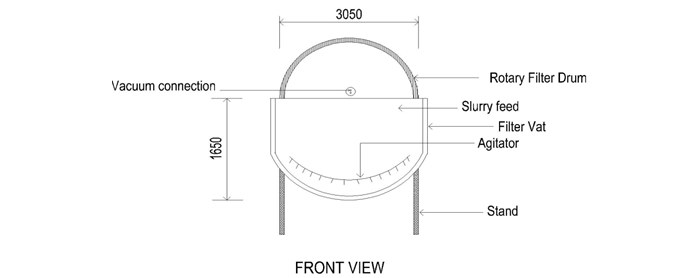
During all process steps, pressure is generated hydraulically via the inlet pipes for the suspension or washing/extraction media rather than pneumatically by means of gas stratification.

The rotary pressure filter operates at a pressure of up to 7 bar (g) and within a temperature range of approx. Variable process pressures and temperatures This means that the rotary pressure filter is also suitable for use in operating scenarios with increased safety or hygienic requirements. The rotary pressure filter is a fully encapsulated unit that can be integrated into production processes in a gas-tight manner. This makes it possible to separately discharge the filtrates or other substances. All process steps take place in separate segment zones within the filter. After separating the suspension into filtrate and filter cake, the rotary pressure filter supports the following additional processes: single- or multi-stage cake washing, displacement washing, counter-current washing, circulation washing, slurrying, solvent exchange, steaming, extraction, as well as mechanical or thermal cake dehumidification. The rotary pressure filter supports a broad range of process steps during a single rotation of the drum.
